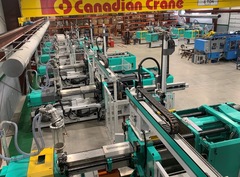
Expanding within their existing property at 165 Line 4 South, MPC has invested heavily in this next step of their growth, all but doubling their injection molding fleet with 18 brand new moulding machines. This fleet expansion includes additional micro-moulding equipment (Boy), significant additional capacity in the 150T to 440T range (Arburg) and a "first-in-sector" application of Cube Injection Molding System (CIMS).
Pre-dating the Pandemic, MPC secured new business from a Global automotive customer to supply a component that is commonly found in BMW, VW, Volvo and Tesla vehicles. Applying their engineering expertise, ingenuity and innovation, MPC has been successful in developing the CIMS technology that successfully won matched funding support from NGEN and FedDev. As part of an all-Canadian collaboration with Niigon Machines, MPC implemented the CIMS concept from the ground up, this state-of-the-art equipment having pride of place in their new facility. Developed and built in parallel as the construction of the building took place, the Cube Injection Moulding System is now operational and will run up to 10 million parts per year thru 2032.
The key for MPC is in the 'how' CIMS dramatically benefits the molding process, slashes cycle time by up to 50% and increases production capacity. This process in Germany - considered the engineering mecca of the world, is being done on two separate machines with semi-manual component loading. The MPC approach takes all of this and achieves volume production in a single machine; simultaneously moulding, loading, cooling and unloading parts from four co-located stations CIMS outputs finished parts in just 15 seconds, 24/7.
"This is a major milestone for us" commented David Yeaman, President and Owner of MPC.
"We have made our name in the contract moulding industry over the last 15 years producing high-quality, performance critical parts for the automotive healthcare, electronics and consumer industries. Our new facility delivers a world-class working environment for our team regardless of their role, as well as much needed office space and additional manufacturing capacity. This allows us to not only continue pushing the boundaries of technology and engineering advancement, but we can also accommodate immediate transfer of tooling in circumstances where our partners or new customers are experiencing capacity or quality issues with their existing suppliers".
The new facility is also a foundation for future advancement, strengthening presence in the manufacture of performance-critical components for the medical and healthcare industries. The new MPC footprint includes cleanroom moulding capability and capacity that has application in multiple sectors. This extension of capability and regulatory enhancement opens the door to new moulding opportunities where the defined cleanliness and full traceability of parts is critical to their application. In support of this direction MPC is already operating under the necessary protocols for compliance to ISO13485 and is expected to gain certification to this standard in Q1, 2022.
The company also recently received significant funding from Sustainable Development Technology Canada (SDTC) for the implementation of a first-in-world initiative, an Integrated Pellet-to-Pallet Advanced Manufacturing system, that vertically integrates cap and bottle moulding, liquid filling and automated packaging for products such as hand sanitizer, the finished being made in a single continuous process. This approach reduces CO2 emissions by 4700T annually, compared to current practices and will also be operated in the expanded MPC facility.
The new manufacturing and office facility provides MPC and their customers with over 70,000 sq.ft.of advanced, Industry 4.0 manufacturing space and is located just 60 minutes north of Toronto. Why is that so important right now? "Concerns with supply chain security, limited container capacity and shipping costs that have quadrupled, are all factors causing OEM suppliers and manufacturers (MPC's customers) to look very critically at their manufacturing base." said Andrew Bird, Director of Strategic Business Development at MPC.
"This is a significant opportunity with MPC's current and new customers who are seriously considering or actively engaged in the localization of manufacturing - bringing their business closer to home to ensure supply chain security and control cost. As less well-equipped competitors or those feeling the financial hangover of the Pandemic are unable to respond and capitalize on these opportunities, Molded Precision Components is ideally positioned with full engineering expertise, world-class plastics moulding capability and most importantly, immediate capacity for the transfer of business."
- 30 -
About Molded Precision Components (MPC)
As part of the MPC family of Companies, Molded Precision Components and sister operation MediCA Healthcare deploy Industry 4.0 technologies to deliver precision engineering and contract manufacturing excellence to both automotive and healthcare sectors.
Established in 2006, the business is focused on medium to high-volume component manufacturing for the most challenging of applications and operates to quality standard ISO 9001:2015. In addition to GMP (Good Manufacturing Practices) certification, Molded Precision Components is ISO/TS 16949 certified for Automotive clients. Likewise, MediCA Healthcare operates under the QA protocols necessary for ISO 13485 for medical device components (certification expected in Q1 2022).
The MPC Family of Companies inspires sustainable advancement, consistently bettering ourselves, our activities, our community & our environment, delivering excellence for our valued manufacturing partners.
GET IN TOUCH
Andrew Bird
Molded Precision Components (MPC)
http://www.mpccomponents.com
You can see the original version and more on PRLeap here: http://www.prleap.com/pr/281378/molded-precision-components-expands-advanced-molding-capacity